The Dunlop Hub
South Island | Commercial Building
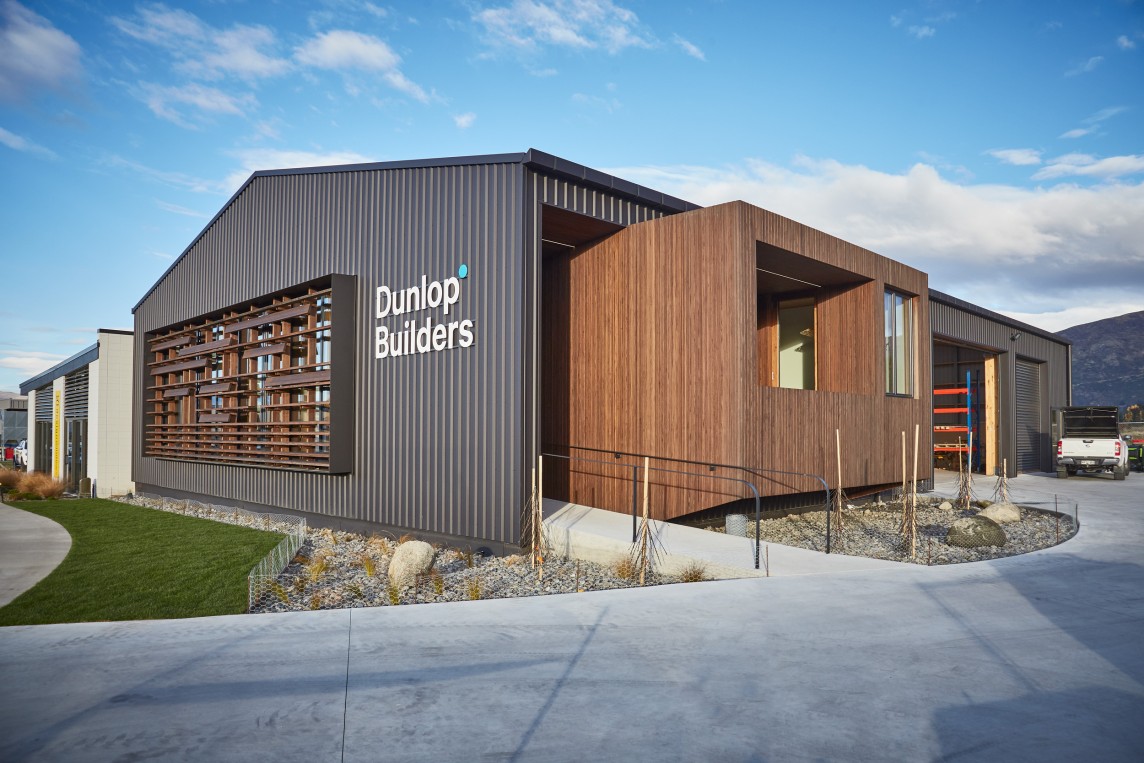
The Hub, the centre of activity for Dunlop Builders, combines elegant architecture with sustainable design principles. The office and workshop spaces reflect Dunlop Builders' commitment to mastery, home, and community. The Hub received Passive House Plus certification, making it the first office in New Zealand to achieve this certification.
Thermal modelling was performed to determine the building's heating demands and thermal performance to achieve high energy efficiency. The result was a heating demand of less than 15 KWH/pm2 and an impressive airtightness rate of .38 air changes per hour (ACH50), well below the standard of 0.6. Proclima provided airtightness membranes and tapes, and Stiebel Eltron provided a mechanical ventilation system.
The ventilation system uses a heat exchanger to transfer heat from outgoing stale air to incoming fresh air, reducing the amount of heating required and maintaining a comfortable indoor temperature. Additionally, the MVHR system helps maintain good indoor air quality by constantly circulating fresh air and removing stale air.
Furthermore, The Hub is powered by 24 Hyundai solar panels installed on the roof, which provide enough electricity to power the office and workshop, as well as charge the PHEV car in the fleet. The Hub also uses triple-glazed, argon-filled, timber-framed windows made by Thermadura in Dunedin.
The design elements working together create an extremely energy-efficient space, and the additional energy produced has pushed The Hub beyond the classic Passive House certification to Passive House Plus! Sustainability was a key factor during the design phase of The Hub. The project team researched and benchmarked products, materials, and methodologies that had sustainable elements. The focus was on embodied carbon reduction, waste minimisation, and using renewable materials.
To reduce the carbon content in the concrete, silica fume was used with the concrete, known for its high embodied carbon. The silica fume replaced a portion of cement in the mix, reducing carbon by around 13%. The use of timber construction also aligns with the project's focus on sustainability and embodied carbon reduction. Timber LVL portals were used for the shed design, and Abodo timber was used extensively throughout the office. The cupboards and kitchen were made from Plytech birch elite plywood, a Declare-listed product free from harmful chemicals.
Waste minimisation and recycling were also important to the project team. During construction, only 2.5 skips of waste were sent to the landfill, and nearly 1.4 tonnes of cardboard, polystyrene, and plastic were recycled. An office composting system was also started, fed with food scraps and shredded paper.
Overall, The Hub is an excellent example of sustainable design and energy efficiency, showcasing the possibilities of green building practices in New Zealand.